Click to listen to this article
|
By Wayne DeCou, Director of Equipment & Engineered Solutions, Volm Companies
The carrot industry is facing a rapidly changing landscape. From sustainability efforts to retailer requirements, the pressures come in many forms. But, as the old saying goes, every challenge is an opportunity. And there are many incredible opportunities with the exciting innovations that are emerging in the industry.
During Volm’s 70-year history, the company has seen its fair share of change. But the advancements happening now are truly unique. As a total solutions partner, we have always understood that we have to think far beyond our packaging. Because of this, we always look at how our equipment can help our customers, particularly when it comes to reducing our environmental impact. From washing, grading and weighing to bagging, baling and palletizing, choosing the right equipment is just as important when it comes to dealing with modern-day pressures.
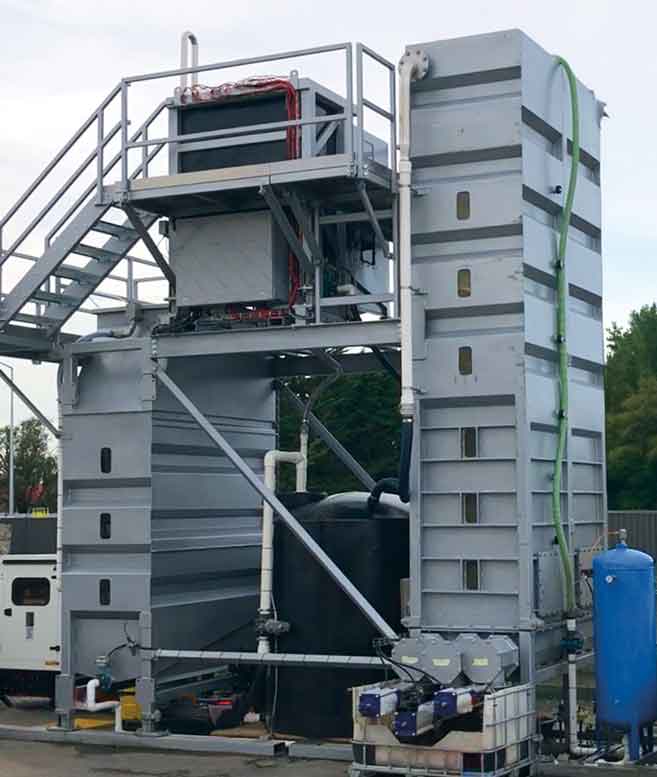
Water Recycling
The carrot industry is experiencing these pressures directly. Water consumption, for example, is an area where many sheds are facing tightening government restrictions and, depending on the jurisdiction, punishing fines. But state-of-the-art technological solutions are keeping facilities ahead of the curve, reducing water volume while improving wastewater quality. These improvements have allowed growers to drive down costs, reduce unnecessary waste and remain in compliance of regulatory requirements for wastewater discharge.
Volm’s latest water recycling system, through our exclusive partnership with Wyma, has been a game changer for the carrot industry. This new system has a small footprint with a big impact and offers a chemical-free solution that eliminates debris, removes soil content and reduces contaminants such as E-coli, nitrates, phosphorus, biochemical oxygen demand, chemical oxygen demand and carbonaceous biochemical oxygen demand.
In stage one, dirty water is pumped from a tank to a micron filter, where filtered solids such as organic fibers, sand and produce are extracted. Pumps send the filtered water back to the process line for recycling, or to the next stage of water treatment, the mud tower. In stage two, fine soils such as silt settle in the mud tower as the water flows across its length. Clarified water then exits the tower via the overflow. Settleable solids are extracted from the base of the tower automatically. These extracted solids can be conveyed or deposited directly into waste bins. The final stage of processing takes place in the ElectroClear system. Here, water is treated to a high level of clarity with no need for added chemicals.
Facilities that have recently implemented this system have reaped immediate rewards. Daily freshwater consumption at one shed plummeted by 75 percent. Another facility was facing limited access to a freshwater supply and would not have been able to have a high-capacity wash line without the use of water recycling to subsidize its operation and overall consumption. These are tremendous benefits that will continue to pay off both financially and environmentally for years to come.
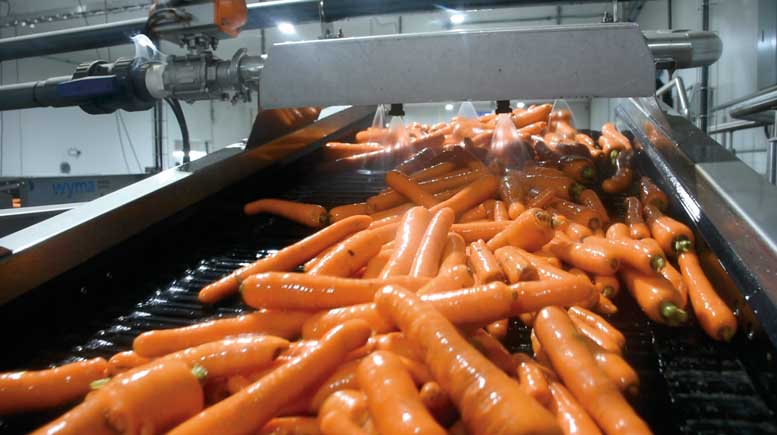
Sorting
Sorting is another area that has seen tremendous strides in technological advancements. To step up our carrot sorting and grading capabilities, Volm, in partnership with Visar, recently rolled out infrared technology as part of our optical sorter. Using 360-degree optical cameras, this sorter simultaneously sizes and grades with extreme accuracy. The latest edition of the infrared technology paired with white LED lighting helps to increase the detection of difficult-to-see defects such as rot and mouse damage. To complement the addition of this technology, the number of outputs on the machine recently increased to 16. Continuous software enhancements have also improved the sorting accuracy and efficiency. These developments have had a tremendous impact on capacity, throughput and being able to sort into different categories. All of these improvements have decreased overhead, increased profits, reduced waste and improved quality.
Palletizing
In palletizing, the headwinds have also been changing. Here, many growers and packers are facing tighter pallet requirements from retailers who are increasingly standardizing their operations. These new requirements are intended to boost efficiency and improve operations – all worthwhile causes that, nonetheless, require more compliance when it comes to pallets. Many conventional palletizing solutions are capable of delivering a high quality stack. These include our VST series of palletizers, which can help sheds easily conform to emerging retail requirements.
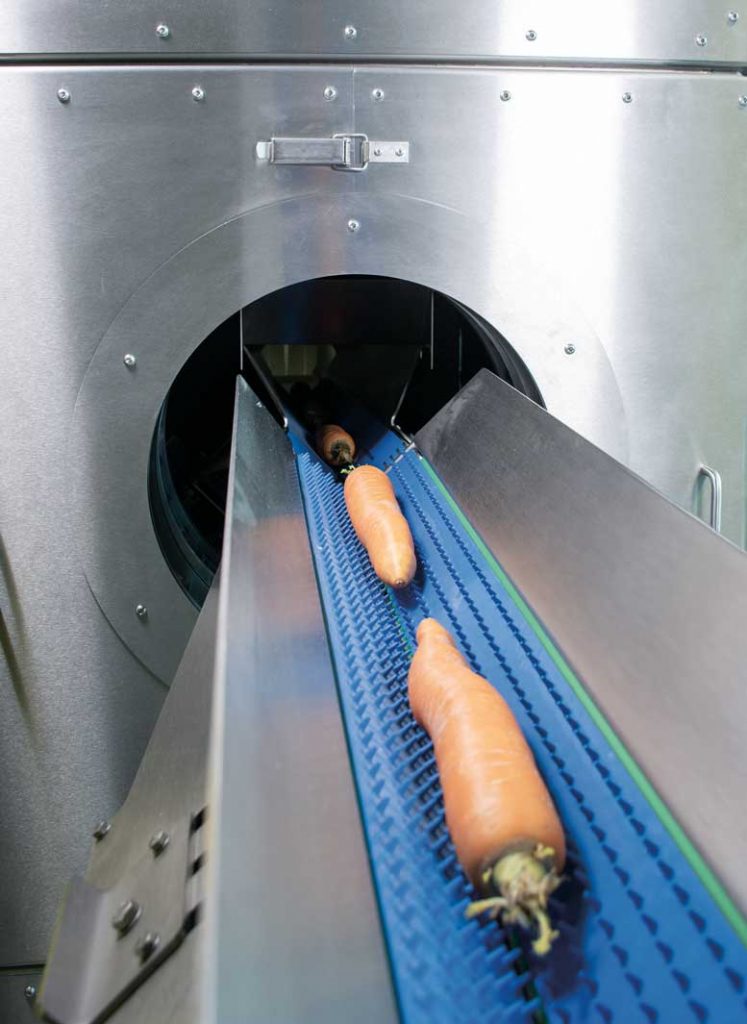
Packaging
Finally, when it comes to packaging, Volm truly believes that innovation must continue to be the way forward. The poly bags we offer for carrots help to lock in moisture and prevent unnecessary food waste. They are fully recyclable. And significantly, as they relate to “forever chemicals,” they’re also PFAs-compliant.
While we remain committed to investing in new packaging solutions, we must also be mindful of the costly realities of doing business. Especially as we continue to feel the lingering impacts from global inflation, we believe in making every possible effort to keep costs down. Those efforts include leveraging strategic partnerships, sourcing competitively and ensuring that our packaging facilities are run as efficiently as possible. Pennies add up to dollars, and those dollars help provide the best value to customers. Staying competitive must remain a priority for everyone.
From packaging to equipment, all of these developments make it an exciting time for the carrot industry. Traditionally, automation has always been touted as a successful method of dealing with costly labor restraints. But as we’re seeing more and more, it is proving to be a highly effective strategy for prioritizing sustainability, reducing waste and meeting shifts in retailer requirements. With this progress in mind, we look forward to continuing to meet the demands facing the carrot industry – challenges, opportunities and all.