Story by Denise Keller, Editor
Photos courtesy Manoj Karkee, Washington State University
With labor coming at a high cost and being in short supply, the agriculture industry is looking for new ways to get the job done.
Currently, researchers from Washington State University (WSU), University of California-Davis and University of Arizona are collaborating to develop robotic weeding technology. This would help growers reduce manual weeding, which is one of the most labor-intensive operations on many vegetable crop farms. It would also improve sustainability, according to Manoj Karkee, an associate professor with WSU’s Center for Precision and Automated Agricultural Systems.
Karkee expects labor availability to become an even greater challenge in the future due to increasing economic activities in Mexico and other countries, as well as uncertainties in the immigration system. Automating tasks such as weeding is necessary to minimize labor costs and keep the industry viable in the long term, he says.
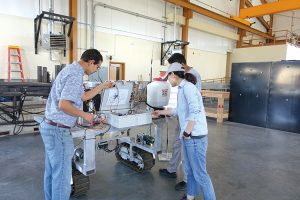
Manoj Karkee (left) and two graduate students inspect an automatic control system that guides the weeding robot through the field.
Progress
The research team is working on a novel concept of using cameras and other sensors to differentiate crop plants from unwanted plants and weeds. When the robotic machine finds weeds, it will either use mechanical tools to remove the weeds, apply chemicals precisely on the weeds or apply heat to kill the weeds. Depending on the type of cropping system and type of weed, one method might work better than the other.
The developers have built the machine at a width of 42 inches and about twice as long, although the width could be adjusted based on specific planting systems. Several units will work together to weed a field in the desired time.
The component technologies are working well, according to Karkee. Now the researchers are putting the systems together. So far, they have integrated the camera system and robotic platform. The prototype also has been integrated with the precision chemical application system, which includes eight nozzles. The researchers are continuing to work on integrating the unit with the mechanical weed removal and thermal application tools.
A team at University of California-Davis tested the technology last year. The research team plans to evaluate the robot in Eastern Washington carrot and onion fields later this year.
Challenges
Right now, the camera and image processing systems can distinguish crops from unwanted weeds with about 80 to 90 percent accuracy.
“It is not 100 percent accurate yet in terms of differentiating the crop plant and the weed because they’re both of similar color. But we not only look at color; we also look at the shape of the leaf. Often times, the shape of the crop leaves is different than the shape of the weed leaves,” Karkee explains. “The sensors have the ability to see a little beyond color. They can look at some of the internal characteristics of the leaves, which might be slightly different.”
Carrots’ unique leaf shape will make it easier to apply robotic weeding technology in the crop, although the close spacing in which carrots are planted makes it more challenging to kill or remove weeds growing in between plants.
Achieving accuracy closer to the 100 percent mark may require the use of additional signals. Researchers are discussing the use of small stakes positioned next to seeded crops or the application of a food-grade coloring to transplant crops to help the sensor system distinguish plants from weeds. They are also looking at treating seeds with a compound that will give the resulting plants a unique color signature that can be detected with the camera system.
“We don’t want to kill even 5 percent of the plants we want or leave 5 percent of the weeds we don’t want,” Karkee says. “There may be situations when we might be missing some percent of weeds if we don’t use any external signal such as applying coloring.”
Depending on the crop and cropping system, the goal may be for the robot to eliminate 95 percent of weeds or better. In other situations, it may be more reasonable to use the robot to reduce weeds to 10 percent and finish the job manually.
“If we can get this robot to work and reduce manual weeding to 10 to 20 percent of where it is today, I think we can make this work for growers,” Karkee says. “In fact, that works for growers quite well because they want to have a certain number of workers throughout the year. They just don’t want to have a very high demand for certain periods of time like weeding.”
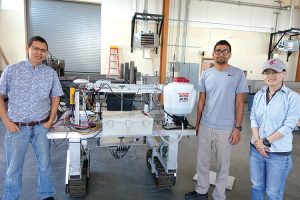
Researchers at Washington State University are collaborating with other universities to develop robotic weeding technology. Pictured, from left, with a research prototype of a weeding robot are Manoj Karkee, associate professor; Kapil Khanal, graduate student; and Xin Zhang, graduate student.
Next Steps
Automated, complex machines require a long development window and multiple years of field evaluation to ensure they achieve the desired performance and functionality in various field conditions. More testing and refinement is ahead before the research team has adequate data and a prototype that a company could commercialize. Toward the end of development, Karkee also plans to complete a comprehensive economic analysis of the technology.
Looking ahead, Karkee predicts that within three to five years, companies may have engineering prototypes of this type of robotic weeding technology. Within five to seven years, growers can expect to see robots in the field. Wide adoption depends on external factors including labor availability, labor cost and whether companies offer the technology as a service or a product sale.
“The size of the farm has also always played a role in the potential to adopt new technologies. That will remain. But rather than having a big 400-horsepower machine covering 20 rows at a time, we are considering multiple smaller machines working together. It creates a model that farmers can adapt to their size,” Karkee explains. “I really feel excited and enthusiastic about what I’m doing and where this is going. It’s a real exciting area.”